Scania cooperation shows promise of remanufactured products
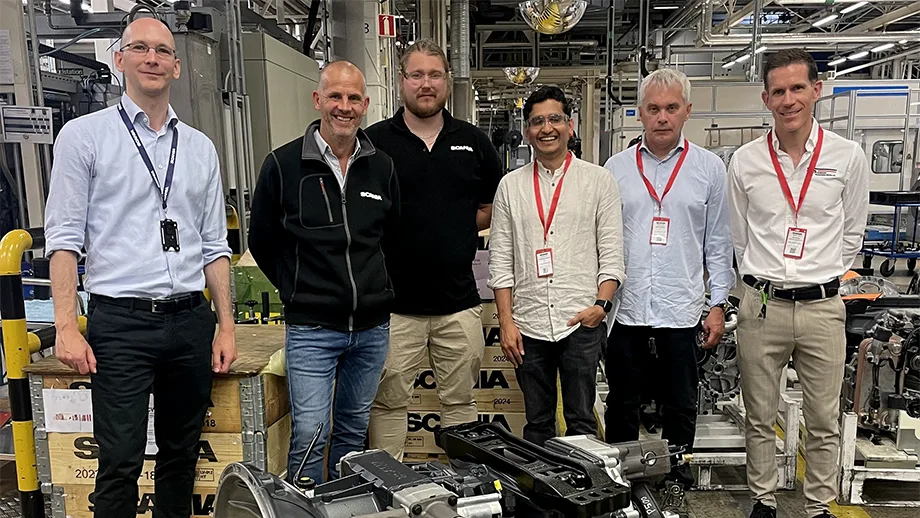
Scania last year made automotive history by incorporating remanufactured components into the production of new trucks. This innovative move, supported by research from KTH Royal Institute of Technology in Sweden, highlights the transformational potential of circular manufacturing systems.
Recognized globally for its expertise in the circular economy, the Circular Manufacturing Systems research group at the Department of Production Engineering at KTH played a key role in the iReGear project. This initiative demonstrated the feasibility of integrating remanufactured components, such as gearboxes, into production lines designed for new products.
KTH researcher Farazee Asif says this approach reduces material consumption by 50 percent and carbon emissions by 45 percent compared to manufacturing entirely new gearboxes.
“More than a decade ago, we envisioned a manufacturing industry where remanufactured components seamlessly integrate into production, consuming fewer resources, generating fewer emissions and reducing costs without compromising quality,” Asif says.
The iReGear project, a collaboration between academia and industry, proved this vision is achievable, he says.
Breakthrough precedent
The project kicked off in September 2023 and concluded in May 2024. While the technical challenge of incorporating used parts into highly automated production lines was significant, the project addressed it by adjusting IT systems and production planning to accommodate remanufactured gearboxes without disrupting operations. Asif says this breakthrough sets a precedent for other industries considering similar transitions.
Beyond technical hurdles, overcoming consumer and manufacturer skepticism about remanufactured parts remains a broader challenge.
“Many consumers perceive remanufactured components as inferior, and manufacturers worry about protecting brand reputation,” he says. However, studies show that remanufactured components often match the quality and reliability of new ones while being 30 to 70 percent less expensive.
The environmental benefits of remanufacturing also align with growing legislative pressures on the manufacturing sector. Directives such as the EU’s Ecodesign for Sustainable Products Regulation promote reuse and remanufacturing, underscoring the legal and ethical case for integrating used parts into new products.
Scania’s collaboration with KTH not only advances sustainable practices but also serves as a model for other manufacturers exploring circular manufacturing systems.
“This project demonstrated a systematic way to scale up remanufacturing, paving the way for a more sustainable and efficient future,” Asif says. “As industries face increasing demands for sustainability, the success of the iReGear project marks a pivotal moment, showing that circular approaches can benefit the environment, manufacturers, and consumers, alike.”
David Callahan
Study circular manufacturing at KTH - an interview with Prof. Farazee Asif
Feasibility Study of Integrating Remanufactured Gearboxes in Production Line of New Trucks