CBH Guidelines for Lab Safety
PROCEDURE
Decisionmaker: Head of School
Valid from: 10 Ocotber 2021
Changed from: 10 Ocotber 2021
Reference number: C-2021-2081 2.1
Responsible for review and questions: Lab Safety Coordinator
1. Purpose
The purpose of this routine is to inform employees about routines and laws relative to lab work.
2. Scope
This routine applies to all employees and visitors who enter the labs at CBH.
3. Definitions
Lab safety rules, laws and routines to ensure safe working practices within our labs.
4. Responsibilities
The Head of the School of Engineering Sciences in Chemistry, Biotechnology and Health (CBH), has the overall responsibility for the proper management of lab safety at CBH.
The Lab Safety Coordinators at KTH have the responsibility to update the document as needed.
The employees at CBH have the responsibility to read and sign the document and to follow the rules and laws described in the document.
5. CBH Guidelines for Lab Safety
The safety guidelines apply to the entire School of Engineering Sciences in Chemistry, Biotechnology and Health (CBH) and are intended to complement information provided by the Swedish government relevant to our working environment. Everyone who is active in the CBH School labs must familiarize themselves with the guidelines and, as needed, relevant Swedish law.
CBH Guidelines for Lab Safety (pdf 429 kB)
Work with Chemicals
Purchasing Chemicals
Chemicals must be purchased through our framework agreement in Wisum and there can be fines associated with breaking this regulation. If a particular chemical or product cannot be found through our framework agreement contact our purchasing manager ( hoki@kth.se ) for help. Be aware, that the buyer is personally responsible for providing safety data sheets for all chemicals purchased outside of our framework agreement.
Permits for Chemicals
Permits are required prior to the purchase of certain chemicals. Additionally, chemicals may require an end user statement, where you as the user must describe what you intend to do with the chemical. The permit or end user statement must be sent in to the supplier before they can approve any orders.
Chemicals that require permits include:
- A and B listed chemicals
- Drug Precursors
- Goods Dangerous to Public Health
- Mercury
- Hydrogen peroxide
Both A and B listed chemicals and drug precursors are marked in KLARA. If you determine that you need a permit, contact CBH Lab Safety ( labsafety@cbh.kth.se ) to help with the process. Included in the application process is relevant risk assessments and justification as to why this chemical cannot be replaced with a less harmful alternative. Keep in mind that it can take months to receive permission following the submission of an application.
Hydrogen peroxide
Work with hydrogen peroxide requires a permit depending on concentration. For hydrogen peroxide with a concentration ≥ 20 %, the following storage volumes are permitted:
- A maximum of 1 litre if the concentration is ≥ 80 %,
- A maximum of 5 litres if the concentration is 60-80 %,
- A maximum of 50 litres if the concentration is < 60 %,
- Keep hydrogen peroxide in a refrigerator due to gaseous decomposition.
Dry ice
Contact with dry ice can lead to burn injuries. Additionally, dry ice should only be handled in well ventilated areas due to potential depletion of oxygen levels in the air. Always wear appropriate insulated gloves and eye protection when working with dry ice.
Radioactive materials
KTH has a common permit for work with radioactive materials from Strålskydds-myndigheten. Within KTH, individual sites where radioactive materials are used must be registered centrally. For additional information please see: intra.kth.se/campus/sakerhet/stralsakerhet
Contact CBH lab safety (
labsafety@cbh.kth.se
) if you plan to set up a new site to begin work with radioactive materials. Additionally, all employees who plan to work with radioactive material must attend a course given by Professor Mats Jonsson (
matsj@kth.se
) who acts as an advisor with regard to the use of radioactive materials at KTH.
Storage of Chemicals
All new chemicals must be registered with barcodes in KLARA prior to being stored in a lab. Chemicals may not be stored in any place other than in a ventilated cupboard or storeroom intended for chemicals.
Reference the safety data sheet for information on correct chemical storage. Special marking is required for flammable and toxic chemicals. General rules regarding storage are listed below.
- Flammable liquids must be kept in ventilated cupboards and must not be stored together with non-flammable toxic substances.
- A maximum of 40 Liters flammable material can be stored per designated fire cell.
- Flammable and toxic chemicals are stored as flammable substances.
- Strong acids must be kept in ventilated acid-proof cupboards (separate from bases).
- Strong bases must be stored in ventilated cupboards (separate from acids).
- Organic substances and strong oxidizing agents should not be stored together with strong acids.
- Ethers and peroxide-forming substances should be stored in the dark and be clearly labelled when the containers were opened and when they must be discarded, as explosive compounds form with time.
- All chemicals that require refrigeration must be stored in spark-free refrigerators.
Medicines and drugs must not be registered in KLARA. Antibodies and proteins do not need to be registered unless they are mixed with chemicals (e.g. sodium azide, a common preservative) or if they are considered harmful according to CLP Regulations (in which case they should have an associated SDS).
Kits, cell media, buffer solutions and gas containers should be registered in KLARA.
Labelling of chemicals
All solutions made must be marked with clear labels. Information regarding the chemical contents, any relevant hazard symbols (as per CLP), the name of the person who made the solution and production date must be included. (See the Swedish Chemicals Agency’s page for detailed information about the classification, marking and packaging of chemical substances and mixtures).
CMR chemicals
When working with chemicals that are carcinogenic, mutagenic or toxic for reproduction (CMR) an investigation into possible substitution must be completed prior to beginning work.
H350: May cause cancer
H340: May lead to genetic defects
H360: May harm fertility or an unborn child
Additionally, a register is kept of any accidental exposure to CMR chemicals. For more information please see KTH Intranet/CMR investigations.
Highly corrosive substances
Strongly corrosive chemicals must not be kept on highly placed shelves. Nor may they be transported or be stored longer term in beakers or flasks. Bottles containing these chemicals should preferably be transported in a plastic bucket or the like.
Safety glasses shall be worn when corrosive chemicals are being transported. A face shield must be used when large amounts are handled, and when tapping from large bottles and diluting.
- Perchloric acid is explosive in contact with organic materials.
- Bottles containing bromine can become brittle after a time, and these bottles shall therefore always be handled carefully
- Concentrated nitric acid can cause a fire when contacting many organic materials. Correct gloves must be worn.
Transport of chemicals
All transport of chemicals must take place in a safe manner and in accordance with the risk assessment. Use secondary containment as a protection against leakage. Avoid travelling in an elevator together with volatile chemicals. We are not authorized to transport chemicals outside our buildings.
Do not travel in an elevator together with gas cylinders or liquid nitrogen.
Products classified as PDA (Produkt med Dubbel Användning) may require special permission if you would like to import or export the product.
Working with Gases and liquid nitrogen
Gas cylinders
Numerous gases contained in cylinders are used in our labs and general guidelines are listed below.
- A gas cylinder may only be connected to a reduction valve with the same name as that given on the cylinder.
- Only the reduction valves and gas tubing approved for the particular gas may be connected to a gas cylinder.
- Gas cylinders must be treated carefully and must not be subjected to shocks or blows or heat.
- A gas cylinder must be placed so that it cannot fall over. It must always be chained fast and the chain must not be placed around the valve or too far down the cylinder. Alternatively, the gas cylinder can be kept on a wheeled trolley. A nylon strap, or similar, is not sufficient protection as it can melt in the event of a fire.
Study the product information and safety datasheet carefully to obtain as much information as possible about the gases you intend to work with. If any question remains, contact the gas supplier. Some commonly used gases and associated information is listed below:
- Oxygen – Oxygen is always stored together with non-flammable gases.
- Acetylene – Gas cylinders larger than 5 litres containing acetylene, which is used with compressed air or oxygen in welding, shall be furnished with a back flow protection device to prevent back flow in the tube system to the gas bottle. The pressure on the regulator must not exceed 1.5 bar.
- The installation shall be checked twice a year and include a leakage test, the test shall be documented. The back flow protection device shall be checked and documented by an authorized person in the annual gas audit. The documentation from these checks shall be available for the staff and supervisory authority concerned.
- Fire protection gloves must be available in the vicinity of the acetylene cylinder in case of a fire.
- Leaking acetylene may smell like garlic if there are impurities present.
- Gasol (LPG) – Cylinders are filled with condensed gas and must not be kept horizontally, otherwise the safety valve can then be blocked by the condensed gas with a risk of an explosion.
Storage of gases
Cylinders containing a flammable or toxic gas must not be left standing in the laboratory. They shall be kept in a special gas cupboard approved for the purpose and be clearly marked with the correct warning sign.
Doors to rooms in which gas cylinders are kept shall be marked with the warning sign for gas cylinders.
Transport of gas cylinders
The carts intended for the transport of gas cylinders shall always be used when cylinders are moved. Do not travel by elevator together with a gas cylinder.
Toxic gases
Gases which are caustic or can cause respiratory paralysis should be purchased in as small bottles as possible, so that they can be placed and handled in fume cupboards when in use, or be placed in a ventilated and fireproof cupboard.
Liquid Nitrogen
The primary risks with liquid nitrogen use are burns and suffocation. Use appropriate personal protective equipment to prevent liquid nitrogen burns including googles and close toed shoes. If the ventilation is out of order, do not collect or use liquid nitrogen. 1 litre of liquid nitrogen can produce 800 litres of nitrogen gas leading to a great risk of suffocation. Never transport or handle liquid nitrogen in an elevator or other areas where there is insufficient ventilation due to the risk of suffocation (storage cupboards, offices etc).
Chemical waste
All chemical waste must be labelled properly and stored in designated containers before being left at the waste station. See this page for detailed information about the chemical disposal routines for your site at CBH.
- Contaminated glassware must be collected in plastic or cardboard containers with a plastic insert. Cardboard containers may not be stored directly on the floor.
- Oil waste is to be collected in a designated container and marked
- Solvent waste containers shall be marked whether the content is water-containing, halogenated or non-halogenated.
- Acids and alkalis must be neutralized before being left at the waste station.
- For radioactive materials, information about disposal must be included in the required permit
Spill kits and waste containers can be purchased directly from SEKA or other suppliers included in the framework agreement for laboratory equipment.
Evacuation is required if a spill is deemed too severe to handle.
Work with Biological Risks
Biorisks are risks associated with biological materials or infectious agents. Examples include toxins, prions, viruses, bacteria, fungi, parasites, cell cultures, blood and tissue, research animals, plants and contaminated laboratory waste. Before introducing a new biorisk to the school, our biorisk risk assessment must be completed and sent to CBH Lab Safety ( labsafety@cbh.kth.se ). Following submission, an evaluation will take place as to whether additional permissions or protective measures are required.
Risk Class
Biorisks are classified into risk classes 1-4 with a higher number corresponding to increased risk. Risk class is determined based on the pathogenicity, mode of transmission and availability of protective measures or treatments.
Risk Class 1: Biorisks that are unlikely to cause disease (no or low individual and community risk).
Risk Class 2: Biorisks that can cause curable or transient diseases (moderate individual risk, low community risk).
Risk Class 3: Biorisks that can cause serious illness (high individual risk, low community risk).
Risk Class 4: Biorisks that are deadly (high individual and high community risk).
Biosafety or Containment Level
Biosafety Levels 1-4 often correspond to risk classes but take into consideration specific procedures used that may alter exposure level and required control measures. The assignment of a level must be included in you risk assessment. The inherent risk of the biorisk being used, the lab space, equipment and routines required for a safe work environment must all be considered. For example, an organism that is classified as risk class 2, may be handled in a containment level 3 lab if high concentrations of aerosols are generated in procedures used.
Genetic Modifications
Genetically modified organism (GMO) – an organism that has been altered using genetic engineering techniques. Permission is required for work with GMO organisms.
Genetically modified microorganism (GMM) – a microorganism whose genetic material has been altered using genetic engineering techniques. Permission is required for work with GMM organisms.
Notifications and permits
Microorganisms
Notifications and/or permits from Arbetsmiljöverket are required before beginning work with wildtype microorganisms belonging to risk class 2 or higher and GMM of all risk classes. Group leaders are responsible for checking the correct permissions are in place for their work.
Invasive Species
Permission may also be required for work with invasive species or the importation of organisms. Invasive species have the potential to cause great damage to the environment. Before importing any organism, check if special permission or containment is required.
Animal Bi-products
Permission is required for work with animal bi-products, contact CBH Lab Safety for more information ( labsafety@cbh.kth.se ).
Common Routes of Exposure
It is important to risk assess the potential of exposure through aerosols, puncturing wounds and skin contact.
Inhalation risks and aerosols – Procedures that may lead to the creation or aerosols include centrifugation, grinding, blending, vigorous shaking or mixing, sonic disruption.
Sharps Usage – One common route of exposure is via injury when working with sharps. Do not attempt to recap, clip or remove needles from syringes. Dispose of all sharps correctly in designated, puncture proof sharps specific waste containers.
Protective Measures when Working with Biorisks
Depending on the risk level of your biorisk material, different protective measures are required. The specific measures required for each procedure must be specified in the risk assessment.
Staff training
All new staff working in spaces with biorisks should receive training on working with biological risks.
Vaccination
All employees that work with human tissues including blood are offered vaccination against Hepatitis B.
Biological Safety Cabinets
Microbiological safety cabinets (MSCs) provide varying levels of protection. There are three different levels of protection, depending on the type (MSC1, MSC2 or MSC3) one uses. It is important to understand the differences in protection level and use the appropriate MSC for your work. MSCs must be inspected yearly to ensure proper functioning.
Handwashing
Hands should be thoroughly washed and disinfected after handling biorisks.
Limited Access
The international biohazard symbol must be present on the doors of rooms where risk group 2 or higher work is completed. Only trained, authorized personal are permitted can enter.
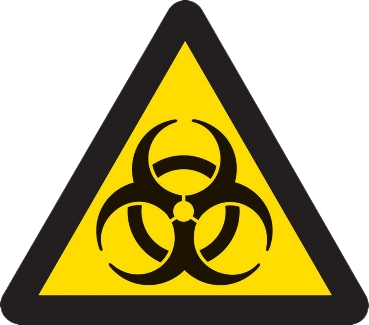
Waste Handling
Biorisk waste including all genetically modified microorganisms and contaminated materials must be either destroyed or sent for destruction with the company procured by KTH to manage hazardous waste at your location. On site autoclaving is the preferred waste treatment for biorisks when possible.
Transport
International and national regulations regulate the transport of infectious substances. It is the responsibility of the sender to ensure applicable rules are followed. Please check the information provided by Folkhälsomyndigheten available at the link below.
Accidents involving Biorisks
A spill plan and spill kit should be available in all labs where biorisks are present. If a spill is too large to manage, close off the space and seek help. If you think that you have been exposed to a biorisk in the lab, report the incident.
Protecting Yourself in the Lab
General Guidelines
- Eating and drinking in the lab is forbidden.
- Working alone in the lab is forbidden.
- Lab coats should be worn at all times while working in the lab.
- Open shoes, shorts and short skirts/dresses are not appropriate clothing for lab work.
Fire Safety
Corridors and stairways are evacuation routes that must not be blocked. If there is a fire in the lab and it needs to be evacuated, make sure to close the door to the lab. Below are signs that mark fire extinguishers and evacuation information.
Fire hazards to avoid in the lab
- Do not store cardboard boxes on the floor in the lab. The material can soak up spillage and magnify a potential fire.
- Electrical equipment should not be stored on the floor in case of leaks or spills. Be careful when using extension to not pull too much power from a single outlet.
- Be cautious when working with volatiles and hot surfaces.
- Emergency exits must not be blocked at any time.
Fire Extinguishers
At CBH carbon dioxide extinguishers are placed in all the laboratories. Powder extinguishers are placed outside the storerooms for chemicals and solvent storerooms. Foam extinguishers are placed in office environments.
Response steps in case of a fire
- Warn – trigger the alarm and inform others in the area, call 112
- Rescue – help others to leave the area if possible
- Extinguish – if safely possible to do so
- Evacuate – leave the building
Personal Protective Equipment
The personal protective equipment required for a particular procedure must be determined in the risk assessment and frequently includes items on the list below:
- Lab Coat
- Appropriate Gloves
- Safety Goggles
- Face shield
- Emergency Shower
- Emergency Eye wash
Personal protective equipment used in the lab must NOT be used outside of the lab. More information about evacuation plans and personal protection can be found in appendix A.
Risks Related to Equipment in the lab
Never use any piece of equipment without prior training. If you notice a problem with equipment, report it to the responsible person and mark the equipment with a sign to warn the next user.
Drying cupboards
Drying cupboards must not be used for flammable items, where there is the risk that the vapour of a hazardous or toxic substance may be emitted or where there may be an explosion risk.
Fridges and freezers
All fridges and/or freezers used for storing any flammables or explosives such as organic solvents must be spark-free because of the risk of fire or explosion.
Electrical hotplates
Electrical hotplates shall always be placed on a base of a non-combustible material. Above the hotplate, there shall be a free height of at least 50 cm. If the temperature is regulated by a thermostat, the cable to the thermostat shall be disconnected when it is not in use.
Water and oil baths
Water and oil baths shall be of metal and fitted with overheating protection. The temperature of use of the oil bath shall be at least 20 °C lower than the flashpoint of the oil.
Vacuum equipment
All glass to be used under vacuum must be intended for vacuum use, made of particularly strong glass, and it shall be fitted with care. In all work with vacuum equipment, protective spectacles suitable for the work must be used. A special shield of shatter-proof plastic should be placed in front of large vacuum installations of glass.
Cooling water tubing
All tubing used for cooling water must be fixed with a clamp or band. PVC-tubing is used for low pressures and a reinforced tube for high pressures. In experiments where there is a risk of fire, explosion or other near-accident if the cooling water suddenly fails, a flow guard is required which immediately switches off the water supply and power supply when the water flow drops below a certain level.
Choose appropriate ventilation
Chemical Fume Hood
Many of our labs are equipped with chemical fume hoods to provide increased ventilation for work with hazardous chemicals. Be aware, that the protection proved is dependent on correct use of the fume hood.
Guidelines for working in the chemical fume hood:
- Minimize disturbance to air flow by shutting doors and limiting movement in and around the hood as much as possible.
- Try to work in the back of the hood and keep it as empty as possible
- Use the brushed holes on the side of the hood for any chords needed for electrical equipment
- The power sockets with a red ring around them are not connected to the ventilation and will still provide electricity in the event of a ventilation failure. Use the red ring power sockets only if the loss of electricity can compromise the safety of the experiment. The other sockets are connected to the ventilation so if there is an electrical failure, the ventilation shuts off and vice versa.
- Leave nothing in the opening to the fume cupboard, which will prevent the window from closing.
- Do not use a fume hood as a storage area.
- The flow rate through a fume hood should be 0.5m/s at all times. If the flow rate goes below this rate an alarm sounds to indicate that the hood is not safe to work in. If the power goes out and the ventilation stops working and the hood needs to be closed by hand.
- The front window of the fume cupboard is not intended to provide protection if the work involves an explosion risk. In such cases, a screen of a shatterproof plastic must be used as protection.
- A vacuum pump which is used in connection with a fume cupboard must not be placed under the fume cupboard unless it is EX-classified (explosion protected). In addition, the pump must be placed in a dish (oil leakage) and this shall be connected to the exhaust (oil fog).
Point exhaust
Place the exhaust as close to the source of contamination as possible. The maximum distance for a protective effect is equal to the diameter of the exhaust channel.
Biological Safety Cabinet
In labs that work with biological risks, biological safety cabinets provide protection from aerosols and splashes.
Storage cupboards
Chemical with any hazard warning should be stored in ventilated cupboards when not being used.
Risk Assessment
Swedish law requires that a written risk assessment be completed before a new experiment is undertaken. The risk assessment must be signed by both the supervisor and the individual completing the experiment and indicates that both parties agree the procedure is of acceptable risk.
Risk assessment templates available in KLARA and on the CBH lab safety website
- The KLARA system has a module for risk assessment of work with chemicals.
- There is also a paper version of the KLARA risk assessment template on the website
- The CBH risk assessment for biorisks is available on the website
- Risk assessment templates BARA and HUMRA are used routinely to assess biorisks at our SciLife campus.
- Risk Assessment in cases of pregnancy and breast feeding employees*
*Inform your supervisor and complete a pregnancy risk assessment of your work with the help of a CBH lab safety coordinator ( labsafety@cbh.kth.se ). Pending the completion of the risk assessment no lab work should be completed.
Medical Controls
In addition to risk assessments and personal protective equipment, medical controls (i.e. blood tests) can be used to control for exposure. Medical controls are required, unless otherwise stated in the risk assessment for work with mercury, lead and cadmium.
Reporting Risks, Occurrences and Accidents
- Risk: a potential problem has been identified
- Occurrence/Incident: something has happened, no one has been injured
- Accident/Injury: someone has been injured
If you have been involved in an occurrence or accident at work or notice a risk, this must be reported. The goal of reporting is to prevent future problems and to thereby improve our working environment. If you would like to make an anonymous report, you can provide the necessary information to a lab safety coordinator ( labsafety@cbh.kth.se ) who will then fill in the report. However, anonymity cannot be guaranteed, if response measures are determined necessary.
At CBH we use the IA system found at the link below to report incidents.
You can also enter the system using the QR code found on the Aj/Oj signs present in labs across the school.
Depending on the nature of the incident, it may be required to complete an external report to either Arbetsmiljöverket or Försäkringskassan. If the incident was an emergency situation Arbetsmiljöverket must be notified as soon as possible but no later than within 48 hours. The IA system will inform you if an external report is required. Be aware, that an injury or illness that is not reported may not be eligible for future insurance coverage if needed. Below is a flow chart illustrating the steps taken during reporting, depending on the nature of the incident.
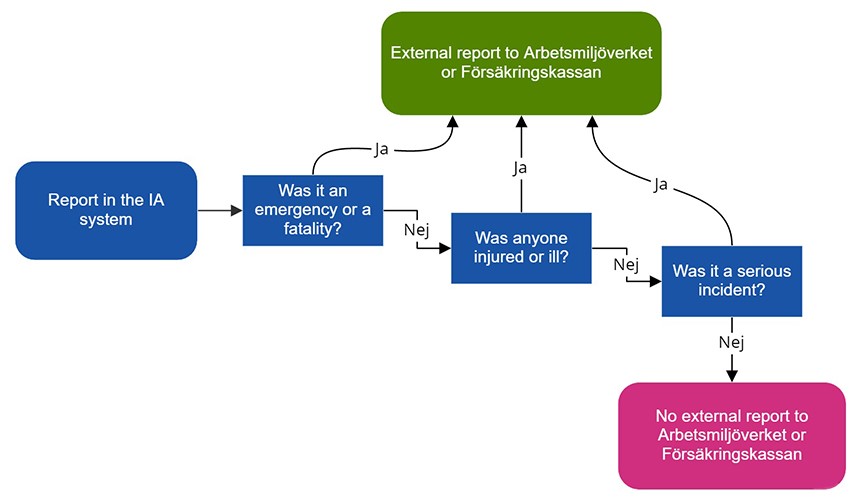
Contact info for emergencies
Swedish Emergency Number 112
Ring this number in case of injury, sickness or fire
Swedish number for medical guidance (Vårdguiden) 1177
Ring this number in case of, for example, suspected exposure to a chemical
Akademiska Hus Alarm 010-557 24 00
Ring this number if there is, for example, flooding in the building
6. Amendments
Approved version | Document date | Amendment | Name |
---|---|---|---|
01 | 2021-10-19 | New routine for lab safety approved. |
Annie Inman |