Chemical Handling at CBH
PROCEDURE
Decisionmaker: Head of School
Valid from: 7 October 2019
Changed from: 7 Ocotber 2019
Reference number: C-2019-0863
Responsible for review and questions: Infrastructure Manager
1. Purpose
The purpose of this routine is to outline guidelines for the handling of chemicals or other substances and ensure they are handled in a systematic, safe and environmentally sound manner in accordance with legal requirements and KTH rules.
2. Scope
The procedure for the handling of chemicals applies to all departments at the School of Engineering Sciences in Chemistry, Biotechnology, and Health (CBH). CBH is spread across 4 locations including, Albanova, Flemmingsberg, Solna (Berzeliusväg 13 and Scilifelab) and Valhallavägen. Additionally, this document applies to the procedure for chemicals at KTH (document ID MR-004).
Purchase, reception and storage of chemicals, laboratory materials and gas.
Handling of chemicals hazardous to health and the environment.
3. Definitions
Handling
Activity or action that involves the manufacture, processing, packaging, storage, transportation, use, disposal, destruction, conversion, sale or transfer of a chemical product or biotechnical organism.
Chemical substance
A chemical element or chemical compound.
Chemical product
Chemical substance or mixture of chemical substances manufactured or extracted whose function is primarily determined by its composition.
Substitution Principle
The principle refers to avoidance of the handling of hazardous substances or chemical products when a less dangerous alternative is possible.
Risk Assessment
A document listing the health and environmental hazards inherent to a specific procedure and outlining risk management measures.
Chemical Waste
Substance or preparation that is intended for disposal.
KLARA
KLARA is a web-based chemical handling system employed by KTH for the handling of chemical products.
CMR-substances
Substances that are carcinogenic, mutagenic or toxic for reproduction. An investigation for less harmful alternatives is required prior to use. Special handling is also required.
Exposure register
Employers are required to keep records of workers exposed to CMRs where there is a risk of ill health. The register must be kept for 40 years.
User
Individual working with the chemical substance.
Purchaser
Individual who orders the goods in Wisum or otherwise.
4. Responsibilities
Sustainability Manager is responsible for:
- Observing legal requirements for chemicals in the field of the environment.
- The Sustainability Manager is system owner of the KLARA chemical system.
- Ensuring KLARA provides the necessary support for KTH to meet legal and internal requirements with regard to the handling of chemicals.
KTH's central KLARA administrator is responsible for:
- Reviewing and approving chemicals in the KLARA system.
- Ensuring that chemical inventories are carried out annually.
- Providing support with regard to the KLARA system including regular information meetings and courses in KLARA.
- Ensuring correct handling of the Exposure registers.
Head of the School of Engineering Sciences in Chemistry, Biotechnology, and Health (CBH) is responsible for:
- Ensuring chemicals are handled in accordance with established procedures.
- Ensuring responsible persons in the field of chemical handling have been appointed and that these persons have acquired necessary skills.
- Ensuring that those handling chemicals receive proper training and information.
- Ensuring compliance with legal requirements for chemicals (e.g. lists of annual uses have been established, lists of persons exposed to CMR substances are established and risk assessments are completed).
- Establishing that permission is available or requested when required.
- Ensuring the school follows KTH's procedures for the purchasing of chemicals.
- Ensuring the exposure register is sent to central KLARA administrators for central diary registration.
- Maintaining ultimate responsibility (ytterst ansvarig) along with the respective division head
Head of division/Group leaders is responsible for:
- Ensuring that risk assessments are completed and updated for all work involving chemical, biological, radioactive or other risks.
- Making certain that new employees get a proper introduction to the safety routines in the lab (for example the policy document, KLARA, risk assessments, waste handling etc.).
Infrastructure manager is responsible for:
- Confirming routines are available and updated.
- Monitoring legal requirements for chemicals within CBH in collaboration with the contact person at KTH Sustainability Office.
The schools responsible for chemicals is responsible for:
- Ensuring the school follows KTH chemical handling procedures.
- Ensuring that users are trained in the KLARA chemical system.
- Ensuring that chemical inventories are carried out in the KLARA chemical system.
- Handling all questions related to chemical use.
- Shall participate in the safety rounds, the part relating to chemical handling.
KLARA-administratoris responsible for:
- Maintaining the school's KLARA chemical system.
- Monitering chemical registration in the KLARA chemical system for accuracy.
The individual completing the inventory of chemicals is responsible for:
- Ensuring that chemicals are added to the KLARA chemical system correctly.
- Adding material safety data sheet (MSDS) into the KLARA chemical system when required.
- Performing a yearly inventory.
User is responsible for:
- Following the school's routines and safety document guidelines.
- Attending courses when necessary.
- Achieving basic knowledge to use the KLARA system.
- Informing the Head of division/Group leader if permission is required for chemicals.
- Adding KLARA barcodes to products entering the lab.
Purchasing Manager is responsible for:
- Ensuring that the school follows KTH's procedures for the purchasing of chemicals.
- Ensuring that whenever possible purchases are made within the framework agreements.
5. Procedure
5.1 Purchase and receiving goods
Chemicals are to be purchased within the KTH framework agreement. If the product is not available from these companies, a separate procurement procedure followed. Please contact the procurement manager before purchasing chemicals outside of the framework agreement.
Prior to purchasing a chemical, the user must check if the chemical has been registered previously and if a corresponding material safety data sheet (MSDS) is available in the KLARA system. If the chemical of interest is not registered in the KLARA system, it is the responsibility of the user to provide information about the chemical and MSDS sheets (in both English and Swedish) to the individual responsible for the KLARA inventory. This must be completed prior to the arrival of the product.
Upon arrival, new chemicals, incl. solvents should be labelled with KLARA barcodes and moved from delivery point to approved storage as soon as possible.
The school is required to inform KTH of the annual consumption of chemicals used in large quantities (eg organic solvents, ethanol). The annual consumption can be calculated using statistics of purchased quantities provided by the suppliers.
5.2 KLARA web-based chemical handling system
KLARA is a web-based system KTH uses for the handling of chemicals.
In accordance with the Chemical Work Environment Hazards (2014: 43), all sources of risk must be identified and listed. All chemicals labeled with a risk pictogram (below) are identified to have inherent risks and dangers. In order for the registration to be current, an inventory must be completed at least once annually.
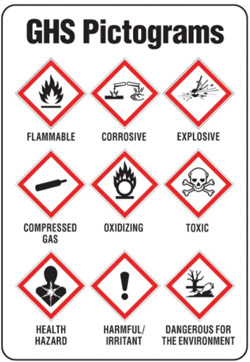
The CBH management team has decided that the module for using barcodes in KLARA should apply to all groups that handle chemicals.
Our register will be updated as new chemicals arrive and shortly after they are finished. Furthermore, eventually we will be able to order chemicals directly through KLARA. Altogether, this system makes possible a more accurate CBH inventory..
Everyone working with chemicals must apply for a KLARA account in order to obtain access. Additionally, at least one person from each group must receive a training course from the KLARA administrator and be assigned inventory responsible. Inventory responsible personal have the ability to add and remove chemicals from the KLARA system through their inventory account.
5.3 Risk assessment
Risk assessments should be performed as outlined in AFS 2014:43 Chemical health hazards and stored in KLARA.
The hazards associated with chemical use including consequences for ones health and potential accidents, shall be investigated and assessed as often as circumstances require.
In addition, such examination and risk assessment (RA) shall always be carried out if experimental procedures change temporarily or permanently or if it can be assumed that the results of the risk assessment will be affected due to new information. Risk assessments must include the entire method/ process, rather than focusing on one chemical at a time, to account for potential synergistic effects.
In order to conduct a risk assessment, it is advisable to begin by looking at the Material Safety Data Sheets (MSDS) corresponding to the chemicals used in the procedure. A Material Safety Data Sheet (MSDS) is a document that contains information describing the potential hazards (health, fire, reactivity and environmental) and outlining how to work safely with the chemical product. MSDS sheets are provided by the supplier for all chemicals and contain guidelines for the use, storage, handling and emergency procedures related to the material. The MSDS also outline how to recognize symptoms of overexposure, and what to do if such incidents occur.
Risk assessments can be performed in the KLARA system or, alternatively made using the “CBH Risk assessment form” that can be found at the CBH intranet. All risk assessments must be signed by the responsible head and kept easily accessible to all personnel within the group.
Each year the CBH infrastructure group will collect information from each department about the progress of the work with risk assessments.
5.4 Use of chemicals
Users of any chemicals should have relevant expertise, this is to be ensured through continuous needs-related education and information.
Users are obliged to take part in the school's and any departmental safety training before starting work in the lab. Read more under Lab safety .
Chemicals must be used in an environmentally sound and safe manner. Before starting any labwork, each user must make a risk assessment based on the entire laboratory process.
5.5 Storage
Chemicals must be stored appropriately. Information regarding storage should be obtained from the MSDS and from the school's safety document “CBH school's safety routines”.
Gases are stored in special gas storage and there are storage facilities for combustible and non-combustible gases. The storage of gases in the lab should be carried out safely, for example in special gas cabinets or carts intended for gas cylinders, always anchored with a chain.
Information regarding who has keys, access / permission for cabinets, rooms or other spaces where chemicals and gases are stored should be established regularly at all of the schools site’s.
5.6 Waste
Chemical waste must be handled in an environmentally sound and safe manner. Routines for waste disposal are available for each campus.
5.7 CMR
According to AFS 2014:43, carcinogenic, mutagenic or toxic to reproduction substances (CMR) should not be used if it is technically possible to use a less harmful alternative. Before using a CMR chemical, an investigation must be made and it must be established that less harmful alternatives are not available.
CMR products are listed with the following hazard statements / risk phrases:
- H350: May cause cancer
- H340: May cause genetic defects
- H360: May harm the fertility or unborn child
- R45: May cause cancer
- R46: May cause hereditary genetic damage
- R49: May cause cancer by inhalation
- R60: May cause impaired reproductive capacity
- R61: May cause birth defects
The CMR investigation shall show whether it is technically possible to replace the product with a less harmful one or not. The CMR investigation must be conducted regardless of the quantity used and options should be sought from several suppliers.
If the investigation shows that it is not possible to replace the CMR product written routines describing how the work will be conducted must be in place and a written risk assessment must be performed before use of the product.
The form for investigation of CMR products, must be completed and sent to the School’s registrar infrastruktur@cbh.kth.se.
General considerations regarding when working with CMR substances:
- Workspaces that may be contaminated with CMR substances should be separated and clearly marked to avoid exposure for personnel not working with CMRs.
- Protective clothing including a lab coat, gloves, goggles and a protective mask are always mandatory when working with CMR chemicals.
CMR Risk assessment
Must contain information including:
- The rooms and spaces where the product may be present and what measures should be taken to inform others that dangerous substances is being used there.
- What safeguards are necessary to minimize exposure.
- What personal protective equipment is required, ie the type of glove etc.
- How the management of equipment, processes or ventilation should be monitored so that early deviations that could increase risk can be discovered.
Always follow the general routines for writing risk assessments.
CMR register
If people have been exposed to a CMR substance, the employer shall establish a register of the exposed persons and the estimated exposure level.
Use the form Exponeringsregister AFS 2014_43
The register shall contain information including:
- The employee's name and social security number
- The employees duties
- A description of the source of the risk the employee has been exposed to
- A measured or estimated degree of exposure
The register must be retained for 40 years and shall be used to detect any correlation between work and disease. The form must be sent to the secretary in the Theme Work Environment, Leif Svanblom ( leif@kth.se ), the original must also be mailed toTheme Work Environment Leif Svanblom, Brinellvägen 8, KTH.
5.8 Radioactive substances
MTH
Radioactive materials are used in very small quantities, when not in use the materials are stored in locked rooms, in locked safety cabinets designed for radioactive materials, with led linings. All radioactive sources used are closed.
Purchasing of radioactive materials is done through KTH’s license.
Before laboratory work with radioactive materials, all personnel should attend a radioactive training and safety course given by KTH’s radiation safety manager If the course is not available in sufficient time, one is given the same course materials and examined by the local lab supervisor.
In labs where radioactive work take place, there is an active dosimeter, and a printed manual regarding what to do if an accident occurs.
6. Attachments
7. Amendments
Approved version | Document date | Amendment | Name | |
---|---|---|---|---|
01 | 2018-04-03 | New routine; due to the school re-organization this document is this routine a merging of the following routines: MR-BIO-134, MR-CHE-200, MR-STH-165 and MR-STH-181 |
Kicki Holmberg |
|
02 | 2019-03-05 | Deleted reference to environmental representative. Dated references to websites on the intranet |
Daniel Tavast | |
03 |
|
Routine moved to a new format. Revision of routine due to a new organization of the environmental management system, in which the environmental representatives’ role is replaced by responsible functions. This document replaces MR-CBH-002. | Sara Pettersson |